- Details
-
Last Updated: Friday, 05 March 2021 23:28
Introduction
Sculpture, ahh, sculpture. Poetry in form and light. I was introduced to bronze and sculpture together in 1980. Coming from a 2-D background where I was employed as a scrimshander (engraving on mammoth ivory), I was initially attracted to sculpture as a way of stretching artistically and bronze as a method of preserving the hundreds of hours I have a tendency of dumping into my work.
The journey that began back then has become the core of my experience. It has led to the founding and operation of North West Artworks, an art casting foundry in Sultan, Washington, that I helped establish with my father and brother. Casting for others has introduced me to many different styles and how bronze relates to them. In my own work, bronze's nature and soul play an important roll in the statement I want to express. My intention for this article is to not ouly illustrate the process of lost wax casting, but also that bronze is more than just a material to reproduce sculpture.
Characteristic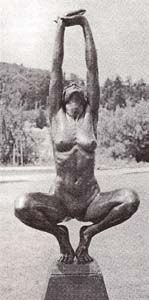
Bronze is 50% to 93 % copper. There are many kinds of bronze and brass alloys, the differences lying in what's been added to the copper to change undesirable characteristics such as low fluidity, gassing and weak castings. Common additions include tin, zinc, lead and silicon.
Most art casting is done in a silicon bronze, a lead-free alloy.Evedur and Hurlaloy are the two types of silicon bronze available. The main difference is the amount of zinc present. Each foundry has its own preference (Evedur being ours), but the desired characteristics are basically the same: fluidity, attention to detail, reparability and finish.
Bronze is bearing metal, which means it is soft and slippery or resistant to surface friction. This gives the metal a unique tactile quality. It is very malleable and can endure pounding and bending (cold work) without tearing.
Bronze is permanent (our insurance company claims it has a life of. 100,000 years at the bottom of the ocean). Bronze is musical (325 Ib. ingot resonates when dropped).
There are many ways of finishing bronze using chemical patinas. Some can accent the form and texture of a piece; others can give a depth of color rivaled only by stone. A faux granite, marble, and sandstone can be achieved with patinas.
Bronze is a structural material making it possible for expanded delicate forms (fingers, etc.) and a great versatility in scale. These and other characteristics make bronze an ideal sculptural medium.
History
Bronze has been linked into the evolution of civilization since its development 5,000 years ago. In the Near East, it was discovered that the addition of tin to copper created an alloy that was extraordinarily versatile in the production of tools, weapons, housewares and art. The lack of tin in the Near East created an expanding trade network that eventually encompassed Europe and the Far East.
The technique of lost wax casting is almost as old as bronze and has remained relatively unchanged until the 1960' s, when high-tech, high-temperature ceramic investment was introduced by the aerospace industry for use in precision castings. This, coupled with the development of silicon and urethane rubber used in the molds, made high detailed casting more achievable. But even with the modern advancements, art castings remain a hands-on, labor intensive, highly skilled craft.
Process
There are two styles of lost wax casting. The difference is in the type of investment in which the wax is encased: traditional plaster investtnent and ceramic shell. Since we use the ceramic shell, the outline below addresses that method:
1. The original artwork is sculpted by an artist in wax, clay. plaster, wood, or stone.
2. From the original artwork (or from a found object), a reusable master mold is made. This master mold consists of a flexible inner mold and a rigid exterior mold or mother mold. The rigid mother mold is designed to hold the flexible inner mold in place and retain its shape. A single master mold can take from three days to several weeks to complete. The flexible inner mold is usually made from polyurethane or silicone rubber and the rigid outer mold from fiberglass or plaster.
3. From the master mold a wax pattern is made using a slush technique (i. e., pouring molten wax into the mold, allowing it to cool slightly and then pouring out the excess wax). This process is repeated several times to achieve the proper thickness (1/8" to 3/16"). Wax patterns for small pieces are usually cast solid. After the wax pattern is removed from the mold, it is chased (correcting in'Iperfections in the wax form) and dissected into pieces to aid in the casting process. This can take a week or more to complete.
4. Wax sprues, gates and risers are added to the wax pattern. They direct the way in which the wax evacuates or leaves the invested pattern and metal enters or fills the ceramic shell, and are crucial in controlling shrinkage of the sculpture as the metal cools.
5. After the wax pattern has been sprued, it is then chemically cleaned and invested (invested means creating a secondary waste mold around the wax). The waste mold consists of a "dip and stucco" technique using a silica slurry with stuccoed layers of imported sand. The result is a fireproof ceramic shell surrounding the pattern and the sprues, gates and risers. One layer of slurry is applied each day for at least eight days.
6. Burnout involves removing the wax pattern from the ceramic shell investment by using heat and pressure. The wax is evacuated when the cerantic shell is flash fired (plunged into an 1800 degree F furnace for 1-112 hours). Hence, the term, "'Lost Wax" .
7. Inspection of the evacuated shell takes place after it has cooled. The shell is vacuumed to remove carbon ash and patched if any cracks were created during burnout.
8. The pour involves melting the bronze in a silicon carbide crucible or cup. The molten bronze is then poured at 1950 to 2150 degrees F into the shells, which have been preheated to approximately 500 degrees F (preheating the shells reduces the chance of flashing and metal shrinkage).
9 The finish work involves:
(a) Knockout, or removal of investtnent;
(b) Degating, or removal of the sprues and gates;
(c) Welding and refabrication of the sculpture;
(d) Chasing the sculpture or fixing any casting flaws;
(e) Cleaning or sandblasting the sculpture;
(I) Patina work or aging, coloring and sealing the metal;
(g) Mounting the sculpture or making the base and fastening the sculpture to it.
Smaller sculptures can be cast in one piece, whereas larger or complex sculptures must be cast in many sections and refabricated. "Temple," an 80% life sculpture (pictured), was cast in seven pieces.
Turn around time is usually four to eight weeks (without mold work), depending on the scope of the project and the work load of the shop.
Costs are hard to generalize, but a 9" solid standing figures runs around $120, whereas a life-sized fignre is in the range of $4,000 to $6,000 without mold work. Costs can be cut dramatically with the artists participating in the labor.
Summary
Bronze offers an artist an expanded arena to express hislber vision. I am conducting a continuing series of workshops (see the paid advertisement in this newsletter) to introduce the fundamentals of reproducing sculpture. The artist can enter at any phase of the workshops to gain experience in a particular area of interest. The workshops are intensive, but give the artist a practical fundamental base on which to build.
Questions
If you have any questions concerning the current workshops or future workshops you would like to see, please contact me directly at: PO Box 777, Sultan, WA 98294; (360) 793-0783. If you need information about having your pieces cast, please contact: Todd Pettelle, clo NW Artworks, PO Box 658, Sultan, WA 98294; (360) 793-2412.
Conclusion
I would like to thank Bill Laprade and Sculpture Northwest for giving me the opportunity to contribute my perspective on this wonderful, though often misunderstood, medium. 1'd also like to express the privilege I feel to be a part of this exceptional organization. Welcome back, Bill.
- Details
-
Last Updated: Friday, 05 March 2021 23:28
Sandstone has been a reliable utility stone throughout the centuries. Many cities, both ancient and modem, take advantage of its fine qualities. It is easy to quarry, found throughout the world, is relatively easy to shape and carve, and resists erosion in most climates. While it is limited in colors, it is commonly uniform, compared to other stones, and therefore provides the architect with a useful building stone.
Geology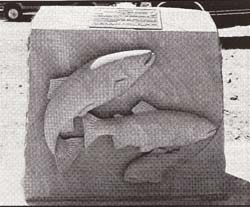
In very basic terms, sandstone is a sedimentary rock that is nothing more than cemented sand grains. If the grain size gets too large, the rock is a conglomerate; if the grains are too fme, the rock is a claystone, shale, slate or argillite. There are several types of sandstone: arkose, arenite, graywacke, orthoquartzite and protoquartzite. The classification depends on the kind of cementing agent and the percentage of quartz and feldspar sand particles. The chief types of cementation include silica (quartz, opal and chalcedony), calcite, dolomite, clay and limonite. The cementing agent can either be deposited at the same time as the sand particles or at a later date.
The sand grains themselves can be derived from any other existing rocks that are nearby, and they may be any shape, although they are commonly rounded to subrounded owing to the collisions with other particles during transportation. They may have accumulated in ancient sand dunes, on river bottoms, in the shallow portion or deltas of fresh water lakes or in a shallow marine environment. Very slowly over millions of years, the deposits of sand are compacted by overlying rock strata. The pressure and the cement cause the rock to gain strength. As a general rule, the older the rock, the higher the strength.
Because sandstone is deposited in environments where organisms live, fossils are common. For similar reasons, concretions, hard nodes with interesting shapes, are also found in sandstone. The concretions themselves are sometimes mined and their interesting shapes are objets d'art.
As a sedimentary rock, it is deposited in layers, and is commonly interbedded with shale, limestone and coal. Where the four repeat in sequences, they are called cyclothems. Where higher depositional energy is involved, the gravel or cobbles change the rock designation to conglomerate.
As a rock (as compared to a mineral), sandstone does not have a designated hardness. Its hardness ranges considerably because of the wide range of cementing agents and degrees of weathering. Caveats aside, sandstone probably ranges from 3 to 6 in hardness. There are, of course, softer sandstones; however, they would probably not hold any sculptural detail and would spall badly in the elements. The hardness of sandstone is nonnally expressed in terms of its unconfmed compressive strength; the strength obtained by compressing a cylindrical piece of the stone to its breaking point. Unconfmed compressive strengths of stone suitable for buildings and sculpture are between 5,000 and 30,000 pounds per square inch (psi). Wilkeson Sandstone is reported to be one of the strongest sandstones in the world. Sandstone weighs between 136 and 166 pounds per cubic foot.
Sandstone is most commonly brown or gray; however, white, yellow, green and red exist. Can you guess what rock type are the "brownstones" of eastern U.S. cities? Some sandstone has layers or streaks of red iron oxide, which may make it attractive for sculpture, but not desirable as a building stone.
Its most common uses worldwide are in buildings, curbstones, bridge abutments and retaining
walls, because sandstone can be quarried relatively easily to very close tolerances. It can be pulverized into sand particles to use as sandblasting material or foundry sand. The hardest sandstones have been used as grindstones and sharpening stones.
Quarrying
Sandstone is extracted in large open pit surface mines, generally from large faces of exposed rock. Because of its stratification, it naturally divides in one dimension. The somewhat horizontal bedding provides a convenient plane on wbich the rock breaks. Planes of weakness in the other two planes commonly develop during compression or tension of the earth's crust. However, these planes of weakness may not be the correct size for building or sculptural stone. Therefore, cutting, drilling and light blasting are sometimes required to remove the stone.
In Washington State, Wilkeson, Tenino and Chuckanut sandstones have all been removed by cutting channels or slots in the rock and then drilling a row of holes aloug the bottom of the channeled rock. A row of drill holes across the back of the channeled section also separates the stone from the mountain. The width of the channels can be varied to render different thickness of slabs or blocks. Feathers and wedges can be used to bring the stones closer to the desired size. Tbe need for carbide or diamonds for the drills is governed by the strength of the cementing mineral.
The rectangular blocks of stone are then milled by gang saws and planers to a predetennined size that closely fits the fmal carved stone. Carvers of architectural stone use a multitude of models to copy.
Working Sandstone
Sandstone is chosen commonly for its uniformity of color and grain size. A unifonn block is essential for a good sculptural stone. Some of the most common flaws in sandstone that are unique to that stone are coal seams, fossils and concretions. In addition to being unsightly, the coal seams are weak and can cause the piece to split. Fossils can either be harder thau the stone or much softer; if softer, they can fall or spall out leaving a hole in the finished piece. Concretions are hard nodes within a softer rock that fonn around a small nuclear particle and bonded with a harder cement, commonly iron oxide. As with many rocks, small seemingly undetected fractures in the stone can result in the splitting of the stone after it has been worked for some time.
Sandstone can be roughed out with a diamond or carbide skill saw. A point can be used to take the shape within about l/2-inch of tbe final shape. Shaping is then accomplished with a toothed chisel, flat chisel and a cape chisel, a narrower version of a flat chisel. A "bull-nose" chisel is used to create concave surfaces. Sandstone carvers have traditionally used wooden mallets instead of iron or steel. The wooden mallets are strong enough to work sandstone and yet they reduce the noise and seem to absorb much of the energy before it reaches the hand and arm.
Smoothing of sandstone can be perfonned witb different implements, depending on the desired final effect. Initially, a carbide scraper or rasp is used, and then final polishing can be done with another piece of sandstone or with a diamond file. The latter is definitely recommended when working with Wilkeson Sandstone.
Sandstone can be either an indoor or outdoor stone, the main differentiating factor being porosity. If the stone has a high porosity, such that water can fill the voids, it is likely better indoors. Left outdoors, moisture and freeze-thaw would soon soften the surface of the sandstone and ruin any details. Look at a piece of sandstone on a building sometime and note the occasional scallop out of the stone facade. Many of the older buildings of Europe require restoration after a century or two. The most effective deterrent is periodic cleaning of the stone.
And remember! Keep your goggles and mask on. The dust is very fine grained and more than likely contains silica. Silicosis can be debilitating and even fatal.
Appreciations
Thanks to stone carver Keith Phillips of Tenino, Washington for sharing his knowledge and expertise of sandstone with us. Keith's enthusiasm for the history of quarrying and carving of sandstone are an inspiration to all who meet him.