- Details
-
Created: Friday, 02 September 2005 03:14
One of the leading lights of the North West Sculptural scene has passed. Although many of you have never met him in person, you have felt his legacy. Everett DuPen was the first instructor invited to the first NWSSA symposium, and is responsible for the beginnings of many of the sculptors that are now the mentors and teachers of our organization. His art lingers throughout the area and the nation, giving us glimpses into his great gift. To Everett, the largest part of his art was in the guiding of emerging artists.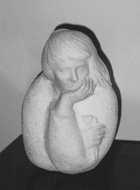
Everett DuPen was educated at USC, Yale, Harvard, and in Rome. He came to the University of Washington in 1947 and ended his career there in 1985, as head of the sculpture department. He was ever indignant that he was forced to retire due to age. That was one of the great disappointments in his life. He went on for many years giving open life model sculpting sessions at the UW in the evenings, using his emeritus status to get a room in the art department. Those of us who attended those sessions experienced the continuing power of Professor DuPen, receiving college level instruction.
Everett’s house was filled with the most amazing collection of art. It was an experience to just visit. There were many of his own works, but also the work of his friends and fellow artists. He used his home as a teaching tool. Each time I visited, there was something else to see and learn. The best part was when we went into his studio, and there he would bloom. We would go on great searches for this or that tool or stone and it could be hours later when Charlott (his wife) would come out and ask if we wanted a drink and to remind us of the time.
Everett did not teach to eat. He taught for the love of teaching. As his student you never doubted his commitment to your growth. You may not have agreed with his analyses of your work, but he was eager to hear what you thought and was never dismissive of your ideas. He wanted to understand them and he wanted you to understand. He would not let you get away with sloppy work or sloppy thinking. If you could explain your reasoning and thought, he was there with direction and guidance. Carelessly done work and disorganized thinking brought his wrath down on you. He expected better of you and he got it. He brought out the best that you could do and more. He was eager to learn from his students, and he rejoiced in our accomplishments.
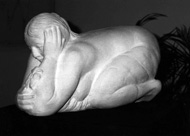
Everett was a good friend to me and I loved him for the twinkle in his eye and his great sense of the ridiculous. He put little stock in his dignity, and some of my fondest memories of him are when he was making a fool of himself. For instance, I have a vivid memory of him being pulled through the closing night party at Camp B on a stone-hauling cart with an oversized zucchini between his legs.
He did not take himself overly seriously but he did take art very seriously. For him, art is the conduit that allows us to better see, appreciate and work in the world around us. To look at one of his figurative sculptures was to see into the soul of man and find that there is good hidden in each of us. His sculptures are reminders that we are here to rejoice in our connection with nature and each other.
The NWSSA and I are fortunate to have been recipients of the teachings of Everett DuPen. We are better for having been exposed to a person of such integrity, grace and dedication.
Everett’s sculptures can be found throughout the northwest: the Seattle Center, Edmonds Art Center, Richmond Beach library, the Seattle Municipal building, the UW library, several local churches and many more places. For more information, go to his website at www.everettdupen.com.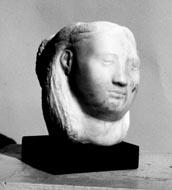
Everett helped to create the Lambdo Rho and art scholarship fund. Memorials can be sent to them and it is the wish of the family that some of those funds will be funneled to NWSSA. The address for Lambdo Rho is: Box 353440 Seattle, WA 98195.
- Details
-
Created: Monday, 02 May 2005 02:36
Swaddled in nylon web dangling from the front end loader of Tom Urban’s tractor, a five foot basalt column moves sideways, its 4x12x26” cut tenon penetrating the upright mortise of a vertical four foot column. Together, they incline onto a bedding slab of limestone. The key wedge is inserted, locking the columns into this relationship for indeterminate time. This group sculpture was the outcome of a gathering of artists and equipment at Jasper Ridge outside Eugene, OR. The weather, food, and friendship had been salutary; the setting majestic; the stone collusive.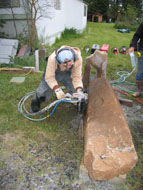
We had been accorded the use of several different models of ICS diamond chain saws. ICS (www.icsbestway.com) has a line of gasoline and hydraulic powered saws similar to wood cutting saws, with water cooling and lubricating the roller nose bar and diamond matrix chain. I had used the gas-powered saws to work on grey granite, comparing cuts with a gas-powered cut-off saw. The cut-off saw is already familiar to most of the NWSSA audience and typically runs a 14-inch diamond blade with water. Cut-off saws weigh in around 30 lbs, are noisy, bulky and gyroscopic in motion. Largely because of familiarity with similar designed angle grinders and diamond blades, they have become a mainstay of many stone sculptors working in larger dimensions. Fret cuts, typically 5” deep and spaced 1 to 2 inches apart on a horizontal surface, can remove large amounts of material quickly. The spinning 14-inch blade can generate considerable kickback and its flywheel effect runs on quite a while after the throttle is released. The cut-off saw is not a tool for tight quarters or timid trimmers.
The diamond chain saw is quite a different tool. Outward appearance similar to wood cutting chain saws is deceptive, since the operation is notably different. The cutting chains of wood saws now have special segments between teeth to prevent kickback and preclude plunge cuts or other tip cutting procedures. The diamond chain does not have cutting teeth to dig in and create kick back, but diamond matrix pads bonded to the chain; it uses the tip of the saw to best advantage. This tip can be inserted into corners, plunged straight through a column, or worked along a surface. The matrix and diamonds grind along the leading edge, the plane surface and both sides of the nearly 1/4 inch wide segment. Once plunged into a surface, the tool grinds at about 5000 fpm wherever the matrix and diamonds contact stone. Full depth on a 14-inch bar means the full length of the chain and the roller nose are grinding stone and pulling power from the saw engine. These saws are hefty (21 lbs), burn some gas (15 min/tank), make considerable noise (100dB), smell, vibration (10m/sec), and spray stone slurry water around a substantial area. They work hard and provide the tool functionality for occasional and remote use.
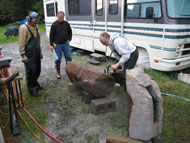
We also had the opportunity to use a couple different models of ICS hydraulic powered chain saws. These saws look like someone shrunk the engine on a gas saw and plugged in a couple of extra water hoses. Light (13 lbs) and powerful (9 hp), different balance with the heavy hoses hanging out behind, smooth (3.5m/sec) and controlled, the hydraulics were performing workhorses in the stone studio. Start with a little soft shoe, get out the whip and they strut out to center circle. Keeping the hoses hanging straight with gravity was a challenge at first, but soon everyone was sighting down the bar and running vertical or horizontal with approval. The basalt column mortise extended beyond the length of the 14-inch bar, so one side was cut with a 20-inch bar from the same side. The other cut was made “blind” from the backside, mating with the original cut about 3 inches deep. Noise was lower (88dB) because the power source for the hydraulic saws is a quiet 15 hp twin cylinder gas powered pump. Sound was similar to your neighbors RV generator during the campout super bowl tailgate at the state park. Actually, any hydraulic source capable of 8gpm will work for powering the saws, like the PTO for a knuckle boom or front-end loader. We were pretty well whipped by the end of the day, but less fatigued than with the gas-powered saws. Noise, vibration, and weight were less, and possibly the cutting power was greater, so the saw did more work. We were also gaining some personal efficiency from work experience during this project.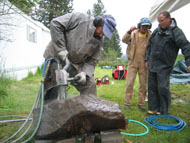
Bottom line, have I bought a diamond chain saw? Not yet. They are amazing tools that perform in a manner like none other. I feel that the chain saw could change the way a person works and thinks about form in stone. That is a rather strong statement, but it stands true in my heart and mind at this time. I extend thanks to those who contributed energy, material and mind to this project: Rich Hestekind, Stuart Jacobson and Tom Urban. Technical and physical accolades go to Tom Monaghan for use and guidance of the ICS saws.
Tom Monahan and his saws will be at Camp B 2005.